AKnarrowback
Well-Known Member
Hi guys!
I might be pulling a "Dr Evil" here and creating something that has existed for the last 30 years. My everyday machine is a 94 XP that I have done a bunch of "custom" things to but have always thought it was really sluggish on the low end with things feeling loaded too heavy. ("Custom" = "you gotta be kidding"). I have already dialed in the carbs, RV cover is machined to spec, all good to go in the running area.
The 140mm pump, with the larger center hub, and the swirl type impellers got me thinking. I'm not sure if there is a larger hub pump that bolts to the original pattern hull (88-94ish). Since the budget is always a goose egg I went McGiver on my pump, had a sleeve 3d printed by a friend and grabbed the JB Weld. The sleeve ID matched the old pump, OD matched a large hub, I cut 6 pieces to match the pump veins, got creative with damming the ends and went to town with the glue. After things cured I spent an hour with the dremmel and a variety of bits to smooth things. It's not perfect, I have a bunch of clean up to do, but the test ride was pretty eye opening.
The only impeller I had was an 11/22 out of a 99 GTI, it needed a bunch of tlc, but it was a lucky shot in the dark. The low and mid range responsiveness is significantly better, top rpms are around 6900, I did not have the GPS but I would guess it is the same or a hair slower.
WooHoo! Sometimes I amaze myself.
Time to pull it apart, mix up more JB to clean up/fine tune the surfaces.
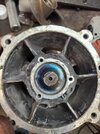
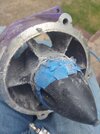
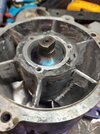
I might be pulling a "Dr Evil" here and creating something that has existed for the last 30 years. My everyday machine is a 94 XP that I have done a bunch of "custom" things to but have always thought it was really sluggish on the low end with things feeling loaded too heavy. ("Custom" = "you gotta be kidding"). I have already dialed in the carbs, RV cover is machined to spec, all good to go in the running area.
The 140mm pump, with the larger center hub, and the swirl type impellers got me thinking. I'm not sure if there is a larger hub pump that bolts to the original pattern hull (88-94ish). Since the budget is always a goose egg I went McGiver on my pump, had a sleeve 3d printed by a friend and grabbed the JB Weld. The sleeve ID matched the old pump, OD matched a large hub, I cut 6 pieces to match the pump veins, got creative with damming the ends and went to town with the glue. After things cured I spent an hour with the dremmel and a variety of bits to smooth things. It's not perfect, I have a bunch of clean up to do, but the test ride was pretty eye opening.
The only impeller I had was an 11/22 out of a 99 GTI, it needed a bunch of tlc, but it was a lucky shot in the dark. The low and mid range responsiveness is significantly better, top rpms are around 6900, I did not have the GPS but I would guess it is the same or a hair slower.
WooHoo! Sometimes I amaze myself.
Time to pull it apart, mix up more JB to clean up/fine tune the surfaces.
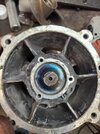
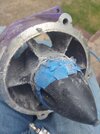
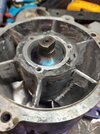