Jack Down Under
New Member
Long story short have tried multiple drill pieces and extractor kits, After getting a quality extractor kit it seems to just eat away at the screw as im not able to drill down any further even with titanium and other metal drill pieces.
Any help greatly appreciated.
Have tried apply heat with a torch have tried making it into a flat head to fit a flat head screw driver piece all no luck and cannot find next to nothing online helping.
2012 Rxtx 260.
Cheers
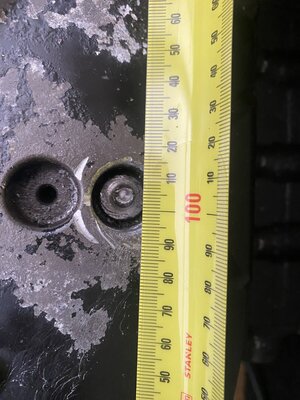
Any help greatly appreciated.
Have tried apply heat with a torch have tried making it into a flat head to fit a flat head screw driver piece all no luck and cannot find next to nothing online helping.
2012 Rxtx 260.
Cheers
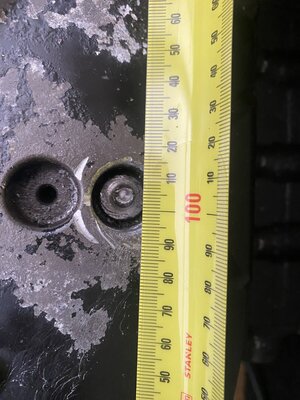