RX951
New Member
:!: Technically, You should do this when the engine is hot, But I from time to time do it when the engine is cold. A hot engine would probably read a few pounds more, but a cold reading will tell you what you need to know.
Run the test on each cylinder one by one.
:!: All the cylinders on an engine should be within ten pounds of each other.
In other words, a three cylinder engine reading 150 PSI, 147 PSI, and 155 PSI would be considered good. If it had 135 PSI, 150 PSI, 150 PSI, it would not be considered good. Something is starting to go wrong with that first cylinder. OK, you have a cylinder that reads low. Is it valves, head gasket or rings, leaking that compression ?
The following are the steps to take to get correct readings.
1. Make sure the battery is fully charged. A battery with a low charge will give low compression readings because of reduced cranking speeds. Youshould maintain 380-420 rpm for a good cranking rpms.
2. Warm the engine slightly for 10-15 seconds to produce metal expansion and to reduce oil drag. A cold engine will give slightly lower readings. But if you take cold readings everytime, it will give you the same baseline.
3. After the engine is warm shut it off and remove all the spark plug wires.
4. Remove one spark plug.
5. Block the throttle open.
6. In turn, carefully insert/thread the compression gauge in each cylinder and with the starter, turn the engine over for five seconds roughly or until the compression gauge has reached its desired target PSI reading.
7. Reinstall spark plug and Repeat these steps for each cylinder.
8. Make a note of the readings from each cylinder. What was the pattern? Does the gauge pump up fast? Is the max reading obtained after five seconds? (Very important)
9. Check the spark plugs from the cylinders with abnormally low or high readings. look for carbon buildup or oil deposits.
10. Replace the spark plugs after each individual reading and torque them to the recommended specs.
Once you've got the readings, it's time to evaluate them to determine just what the future of your engine is going to be.
If the gauge pumps up slowly, such as 30, 50, 70, 90, etc. to an almost normal reading, you probably have ring problems. A general rule is that a maximum reading should occur after two-three seconds. If oil is added to a low reading and the pressure improves, this will confirm worn rings. A persistent low reading generally indicates head gasket sealing, worns rings, scored cylinders or valve problems.
Oil lost through worn valve guides will not be determined through compression testing. Low readings can also be caused by a warped head and occasionally, two cylinders will have very low compression which can be the result of a blown head gasket.
It is important to remember that the addition of oil to the combustion chamber will not improve the compression readings if your engine has burned, warped or stuck valves. High compression readings can be the result of carbon buildup or head surfacing.
Generally, if the variation between the cylinders is 5 to 10 lbs., this is acceptable, but always check the specs in the manual. It would seem that equal pressure is necessary to have smooth running engine, but it's been found that with only 70% of normal pressure is enough for running smoothly. Also, manufacturers specs usually list a bottom line acceptable pressure and a good engine will usually read 20 to 30 psi over the acceptable readings.
If you find that your engine has good compression, it may be time to go back over your tune-up steps. On the other hand, if you've found low compression readings, it's probably time to have that "high hour" engine rebuilt.
:coolgleam: Compression guages can be found at most auto part stores, hardware stores, ebay and other internet sites.
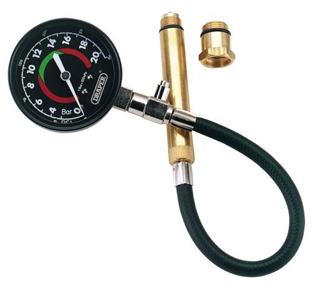

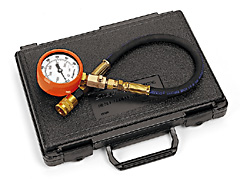
A short rundown of the testing procedure
- Make sure the engine has been warmed up before beginning the test, to ensure that the oil has been warmed up. A cold engine will not test correctly.
- Disable the ignition module or coil.
- Insert the compression tester into one cylinder spark plug hole at a time.
- Hold the throttle to full open position to ensure the engine gets adequate air intake.
- Crank the engine continually for at least five to 10 full revolutions to obtain an accurate reading on the compression tester.
- Record the reading for each cylinder. If any of them vary 10 percent or more from each other a problem may exist in one or more cylinders.
- If the variance is greater than 10 percent, specialized testing equipment may be required to fully diagnose the problem.
- If all cylinder readings are within 10 percent of each other, no further testing is required and compression is considered optimal.
Last edited by a moderator: