I put a second battery in my Challenger 180, just thought I'd post some pictures for those interested. I have noted that some have glued the second battery tray in with Liquid Nails, but I wanted to do something a little more factory, so I got an original tray, and installed it with screws just like the original. I put rivet nuts into the fiberglass for the screws to thread into. The rivet nuts are set into epoxy to give some added strength especially against twisting, and to seal the holes from water. Now I just need to swap the switch to the OFF-1-2-BOTH one that I already have and get and install cables and I'll be done.
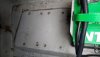
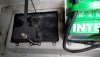
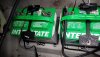
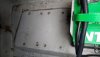
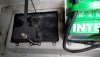
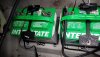